Looking into the future of photonics and exploring the potential of laser technology
At the previous “2024 International Laser Technology Conference (AKL’24),” 525 participants from 21 countries not only participated in 3 forums and 9 sub-venues with a total of 82 expert reports but also visited the exhibitions of 58 companies and 60 laser technology live demonstrations in the laboratories of Fraunhofer Institute for Laser Technology (ILT) and RWTH Aachen University.
During the conference, different forums and conferences focused on the hot areas of current industry concern. At the same time, AKL represents professional depth. It builds a bridge between applied research and practical applications. Technology suppliers and customers come together to jointly raise questions, goals, and visions and promote cooperation through the conference.
The potential of laser technology is far from being realized.
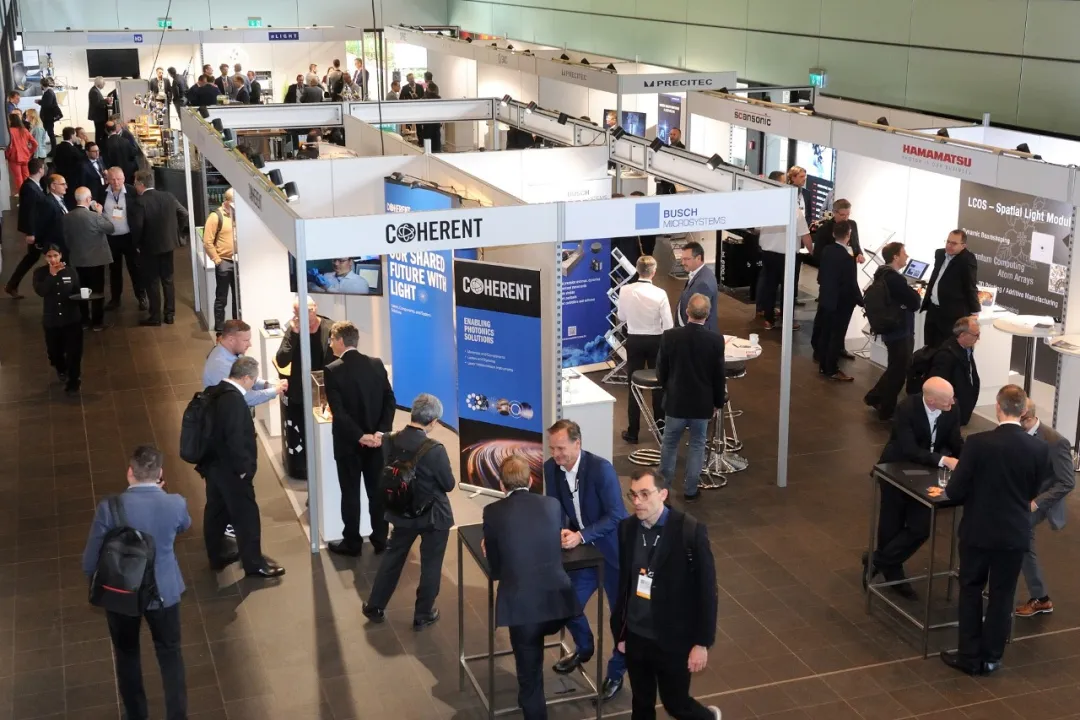
Now, lasers are increasingly used in surface technology, additive manufacturing, and medical technology. Lasers can cut and connect metals and plastics, generate three-dimensional microstructures inside glass, and can be used to produce micron-level semiconductors and electronic products. However, in the sixty years since the invention of the laser, the laser industry has only exploited a fraction of its actual technical and economic potential. The laser has not yet been fully developed.
As Professor Constantin Haefner, Director of the Fraunhofer Institute for Laser Technology, said in his closing speech at AKL’24, “On the contrary, the laser technology has only just begun.” To fully tap its potential, new beam sources, improved optical systems, and optimized processes are needed. The first laser applications were like a crude hand axe, while today’s quantum technology operates on the scale of individual photons, ions, and atoms. Surface technology and optical coatings have achieved similar precision.
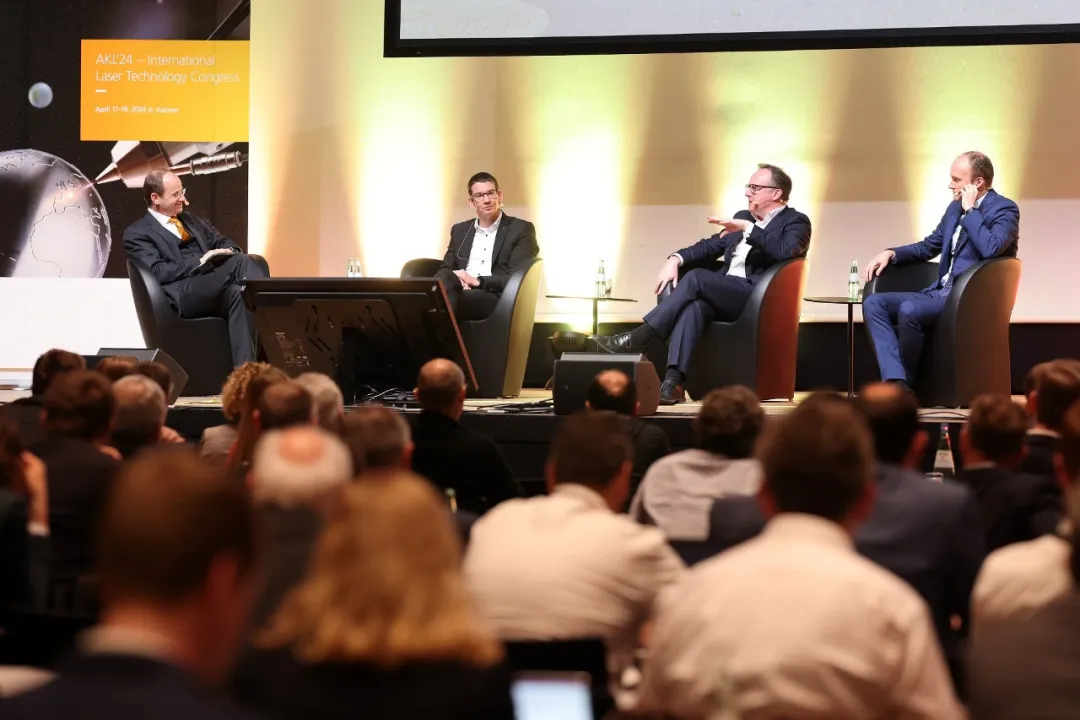
Artificial Intelligence
An important topic of AKL’24: How can photonics use the potential of artificial intelligence as quickly as possible? Due to the increasing digitalization of processing chains, more and more networked machines and sensors are generating large amounts of data. This applies both to research, development, and design, but also to photon production and the product life cycle. Artificial intelligence and machine learning provide new opportunities for refining the rich data raw material.
Data raw material becomes information with added value.
Artificial intelligence is becoming a data-based tool for photon production. The question now is how suppliers of laser systems, sensors, and optics can exploit their technological and economic potential as quickly as possible. Professor Constantin Haefner, Director of the Lauenhof Institute for Laser Technology, said: “With the help of artificial intelligence, the ability to acquire data and derive added value from it has become synonymous with competitive advantage.
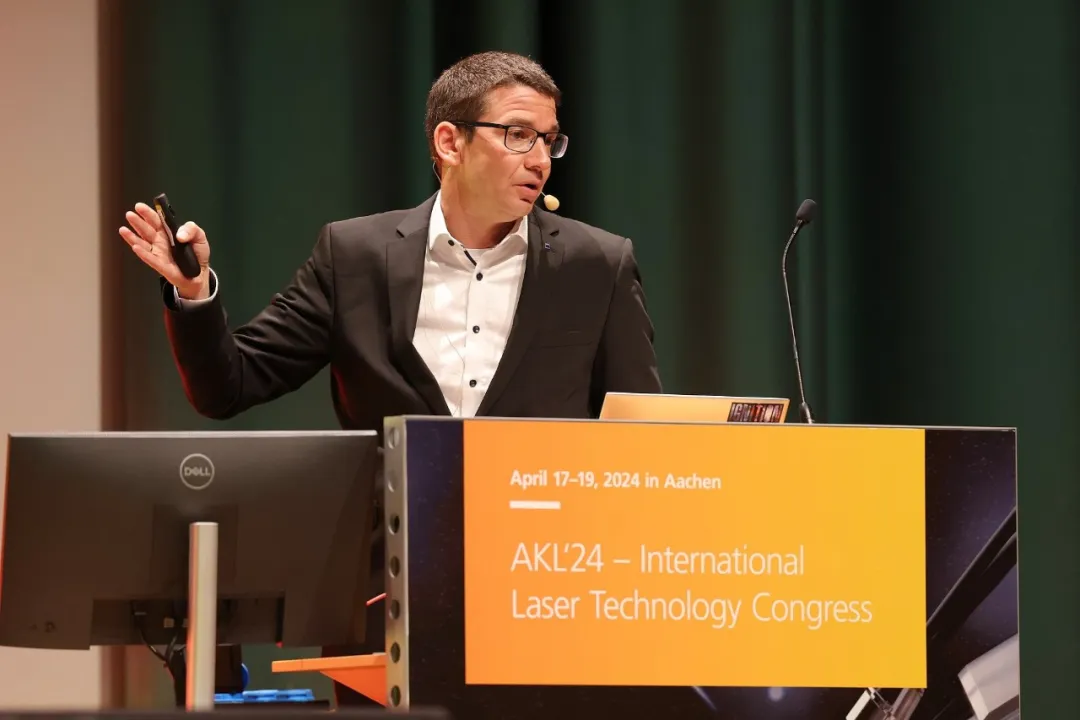
Digitalization and AI are shaping the photonics practice The discussions at the forum clearly demonstrated that combining AI methods with different measurement and sensor technologies, including cameras, pyrometers, or photodiodes for recording process radiation, as well as OCT optical coherence tomography and laser acoustic sensors, offers possibilities that go far beyond the conventional detection and recording of defects and deviations.
If the generated measurement and sensor signals are synchronized with process and system data (e.g., performance data of the laser) by using time, AI-supported analysis methods can also be used to determine the causes of defects and deviations. This would be the first step to readjust parameters in the ongoing laser process so that quality defects are avoided or at least detected immediately. In this way, photonic production processes will be very close to the goal of zero-defect manufacturing.
Since the channels can be combined as required, the sensor also records acoustic emissions, humidity, air pressure, and temperature. In addition, since it can be connected to any third-party sensor system, this compact device can generate a huge database with about one million samples per second.