How does Estun enable fast and efficient welding in automobile manufacturing?
From September 24 to 28, the 24th China International Industrial Fair was held at the Shanghai National Exhibition and Convention Center. At this exhibition, Estun, a well-known domestic industrial machinery company, exhibited aluminum welding, spot welding, and laser welding workstations. How do these workstations achieve fast and efficient welding in automobile manufacturing? It is reported that in response to the market demand for high-quality and efficient production in industries such as automobiles and new energy, Estun has relied on advanced technologies and solutions to work with partners to create benchmark production lines, achieve comprehensive upgrades in efficiency, precision and intelligent production, accelerate the transition from manufacturing to intelligent manufacturing, and provide strong support for the transformation and upgrading of the high-end equipment manufacturing industry. Estun welding robots are continuing to lead the industry’s automation innovation with their high speed, high precision, high efficiency, safety, and friendly and easy-to-use characteristics.
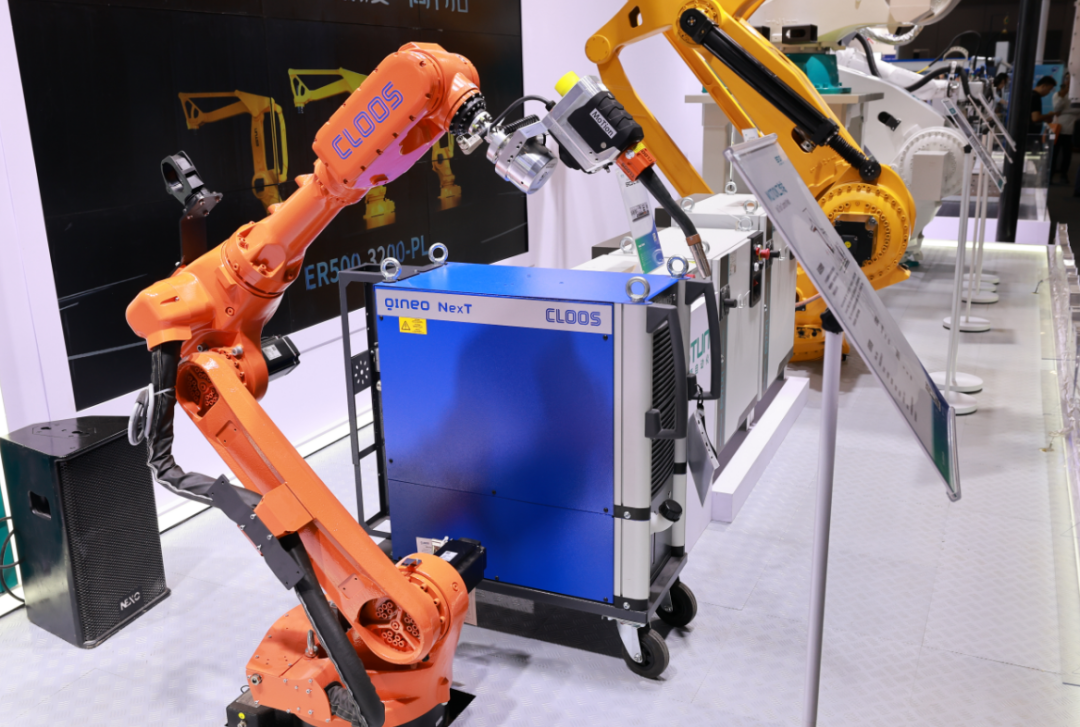
In the field of automobile manufacturing, as lightweighting becomes more and more popular, aluminum alloys and ultra-thin materials are used more and more, and the difficulty of welding has also increased, and dynamic control welding can easily cope with it. MoTion Control Weld (abbreviated as “MCW”) uses short arc control technology with a wire buffer device. This process is innovative based on the classic short arc process control welding “Control Weld”, combined with a mechanical unit to achieve high-frequency wire feeding and retraction. Compared with the traditional short arc process that cannot retract the welding wire, MoTion Control Weld has significantly lower energy consumption and is cleaner to form a short circuit. In general, this process has low heat input, extremely low spatter, and extremely fast welding speed, so it is most suitable for thin plate welding.
In the field of automobile manufacturing, traditional spot welding operations are highly dependent on manual operation, which is not only labor-intensive, but also difficult to ensure the consistency of welding quality, especially welding operations on complex curved surfaces and narrow spaces, which places extremely high demands on workers’ skills. With the accelerated pace of automobile model updates, production lines need to be frequently adjusted to adapt to the welding needs of different models, which greatly tests the flexibility and rapid response capabilities of production lines. In the face of the market demand for high-quality and efficient production in the automotive industry, Estun customized and developed the UNO series of spot welding robots, which meet the needs of efficient, stable and intelligent body spot welding scenarios with the advantages of high rigidity, high performance and high protection, and help automobile manufacturing achieve high-level welding, which can significantly improve the welding production efficiency and product quality of the automotive industry.
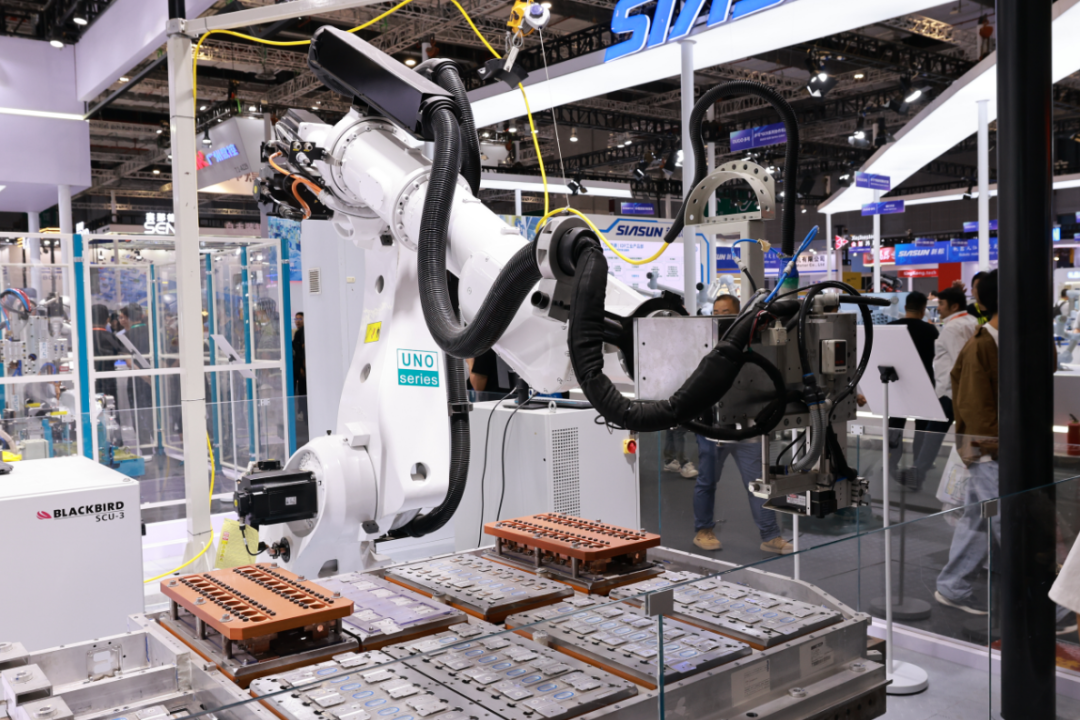
With the booming development of the electric vehicle market, the demand for lithium batteries continues to grow, and the requirements for lithium battery production efficiency and quality are also getting higher and higher. Take Busbar as an example. As an important conductive connection component in lithium batteries, its welding quality is directly related to the safety and performance stability of lithium batteries. However, the traditional fixed-point welding method has problems such as low efficiency and unstable quality, which makes it difficult to meet the needs of large-scale production. ESTUN robot automation welding solutions help the world’s leading power battery manufacturers to help them solve the dilemma of fixed-point welding and improve production efficiency and welding quality. No matter how the traditional Busbar welding process is iterated, it essentially requires third-party vision or PLC to actively initiate position information, the robot to address, and there will always be a pause in the beat to wait for welding time. Flight welding is a qualitative change in the process. The robot trajectory movement is synchronized with the galvanometer scanning position in real time, and the welding position is dynamically corrected through the feedback of real-time visual detection. The galvanometer is based on the robot’s real-time trajectory and compensates with visual data to achieve non-stop welding.
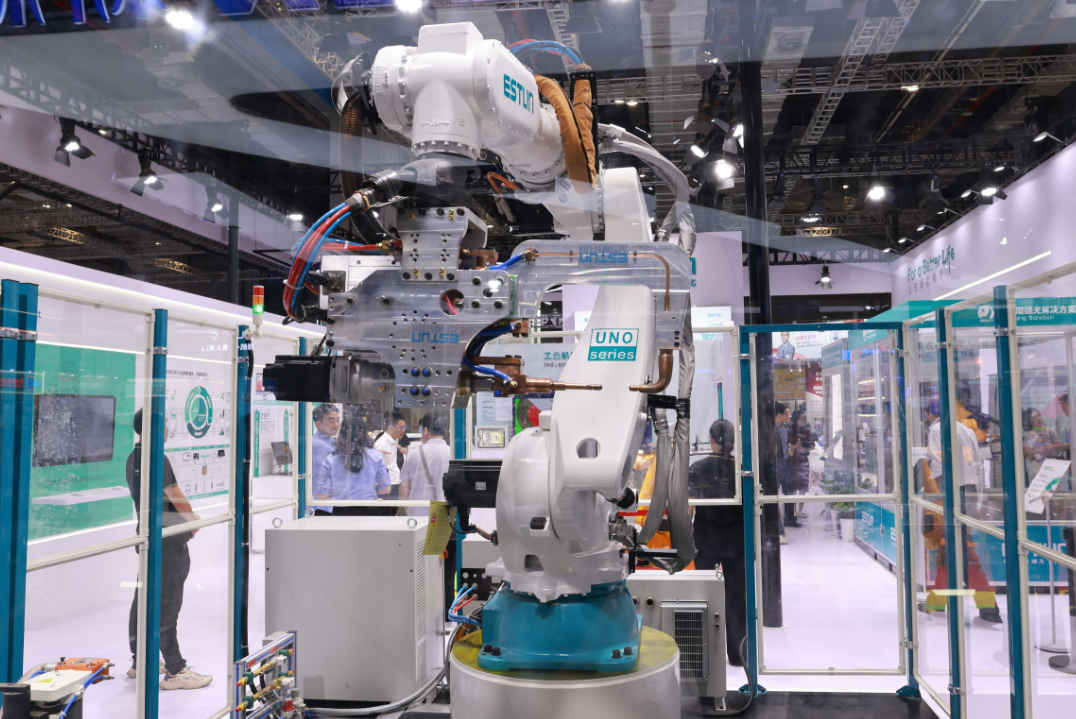
In the automotive industry, especially in the arc welding process of core components such as battery trays, instrument panels, seats, front and rear subframes, non-load-bearing chassis, and anti-collision beams, there are industry pain points such as unstable welding quality due to diverse materials, low production efficiency, difficult to control welding deformation, insufficient automation, high costs, and environmental health impacts. These pain points directly affect production efficiency, product quality, and cost control. The QWAS ECO welding robot created by Estun’s subsidiary CLOOS targets the pain points of the automotive welding industry, adopts low-spatter dynamic welding technology and laser recognition adaptive technology, significantly improves welding quality and efficiency, reduces production costs, and promotes the transformation of automotive manufacturing to intelligence and greenness, effectively solving industry problems.