Factors affecting the quality of laser cutting processing
The quality of laser cutting processing refers to the accuracy of cutting dimensions and the quality of the cutting surface. The surface quality of cutting is generally measured by the following four indicators: incision width and incision surface roughness; width of the heat-affected zone; corrugation of the incision section; and whether there is slag on the incision section or lower surface. The main factors affecting the surface quality of laser cutting are as follows:
1. Laser for cutting: laser should have high beam quality. Laser cutting is a processing based on thermal effect. In order to obtain high power density and fine incision, the focus spot diameter should be small. At the same time, in order to ensure the consistency of quality when cutting in different directions, the laser beam should have good rotational symmetry and circular polarization around the optical axis and high emission direction stability to ensure that the focus spot position is stable and unchanged. Modern lasers should also have continuous and high-repetition output fast switching functions to ensure high-quality cutting of complex contours.
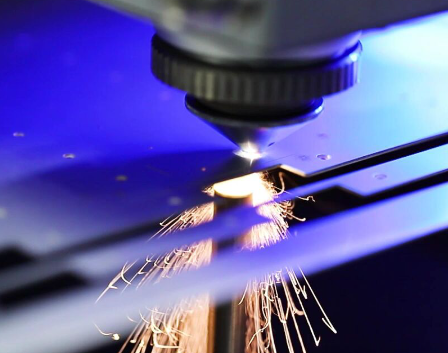
2. Focusing lens and plate thickness. The focal length of the lens is selected according to the thickness of the material to be cut, taking into account the focus spot diameter and focal depth. If the material is thick, the focal length should be large; otherwise, the focal length should be small. The focus spot position should be close to the workpiece surface, and generally the focus falls on the upper surface of the plate, about 1/3 of the plate thickness below.
3. Airflow and nozzle. The airflow in the laser cutting machine has the function of blowing away the molten material, protecting the focusing lens, and even providing part of the cutting energy. Gas pressure and flow are important factors affecting the cutting quality. If the pressure is too low, the molten material at the incision cannot be blown away; if it is too high, it is easy to form eddy currents on the surface of the workpiece, which weakens the role of the airflow in removing the molten material. Practice has shown that the nozzles of different structures will also have different effects on cutting.
4. Laser cutting outsourcing processing cutting speed. The cutting speed depends on the power density of the laser and the thermophysical properties and thickness of the cut material. Under certain cutting conditions, there is a reasonable cutting speed range. If the cutting speed is too high, the incision slag cannot be completely cleared or even cut through. If the cutting speed is too low, the material is overburned, and the incision width and heat-affected zone are large.
5. Cutting trajectory. For the cutting of parts with complex contours or inflection points, due to the change in acceleration, it is easy to cause overheating and melting at the inflection point to form a collapsed angle. Therefore, a reasonable cutting trajectory is one of the effective ways to avoid this phenomenon.